How To Properly Maintain Industrial Refrigeration Systems
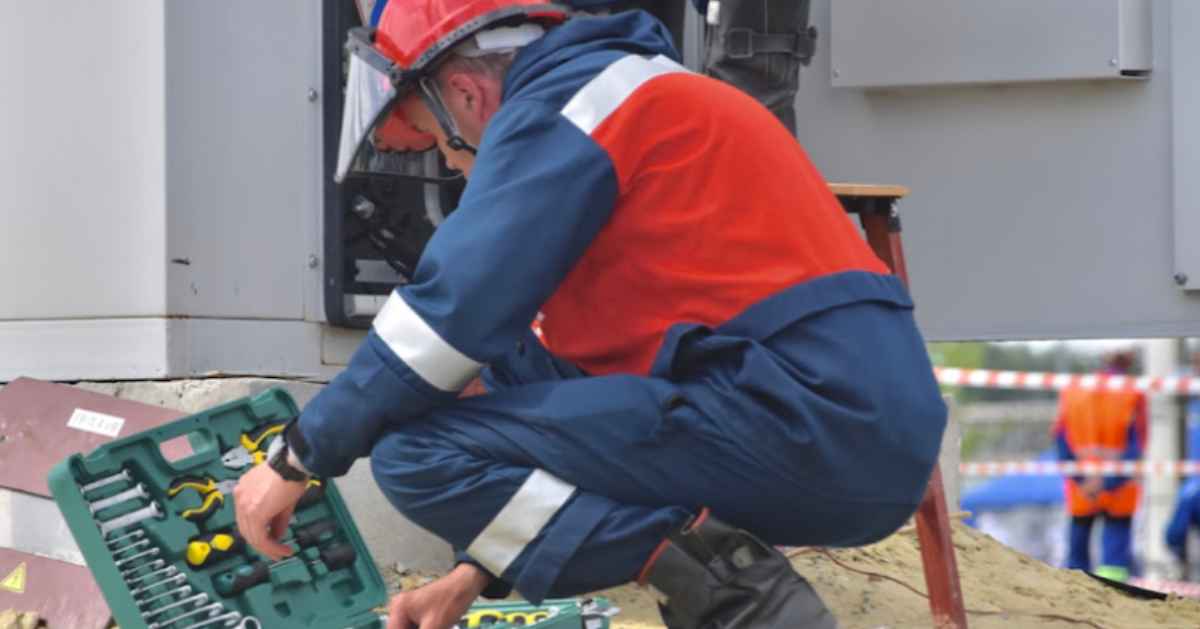
Maintaining industrial refrigeration systems is a crucial component of ensuring the longevity and efficiency of these vital units. With the myriad of components and the sophistication of technology involved, proper maintenance goes beyond simple cleaning tasks. It encompasses a thorough understanding of the system’s operation, regular inspections, and strategic planning for energy conservation. Keeping these systems in peak condition is not just about immediate performance but also about preventing future downtime and costly repairs. Below, we explore the essential steps and best practices to keep your industrial refrigeration system running smoothly.
Understanding the Basics of Industrial Refrigeration System Maintenance
At the core of industrial refrigeration system maintenance is grasping the fundamentals of how these units operate. Refrigeration systems are composed of several key components such as compressors, condensers, evaporators, and expansion valves. Each part plays a significant role in the cooling process and requires specific maintenance procedures. Investing in quality equipment from reputable retailers like Genemco and understanding the function of these parts helps in diagnosing potential problems and provides a basis for implementing a consistent maintenance routine.
It’s also imperative to keep abreast of the refrigerant levels within the system. Over time, refrigeration systems may experience leaks or decreases in refrigerant, affecting industrial efficiency. Regular checks help ensure the unit operates within the manufacturer’s specified refrigerant levels. Moreover, understanding the refrigeration cycle enables maintenance personnel to recognize anomalies in temperature or pressure readings that could indicate a malfunctioning system.
The use of technology in monitoring system performance has greatly enhanced maintenance practices. By installing advanced sensors and diagnostic tools, technicians can gather real-time data on system operations. These technological advancements allow for proactive problem-solving, instead of reactive responses to system failures. As such, training in using these technologies is integral to the modern maintenance of industrial refrigeration systems.
The Importance of Regular Cleaning and Inspection Routines
Regular cleaning and inspection are at the heart of effective industrial refrigeration maintenance. Dirt, debris, and ice build-up can greatly reduce heat exchange efficiency in the system’s components. For example, a dirty condenser coil requires the system to work harder to dissipate heat, leading to increased energy consumption and the potential for overheating. Structured cleaning routines help mitigate these risks and prolong the equipment’s life span.
Inspection routines also play a pivotal role in preventive maintenance. Through methodical inspections, issues such as refrigerant leaks, abnormal noises, or signs of wear can be detected early. This allows maintenance teams to address minor problems before they evolve into major malfunctions. A systematic approach to inspections can also help identify patterns or recurrent issues, leading to better troubleshooting strategies.
Environmental considerations also dictate the need for consistent cleaning and inspection routines. Industrial refrigeration systems typically operate in challenging conditions and may be exposed to various contaminants that affect performance. Regular cleaning limits the environmental impact on the system, while routine inspections ensure environmental regulations regarding refrigerant emissions are met.
Addressing Common Issues in Industrial Refrigeration Systems
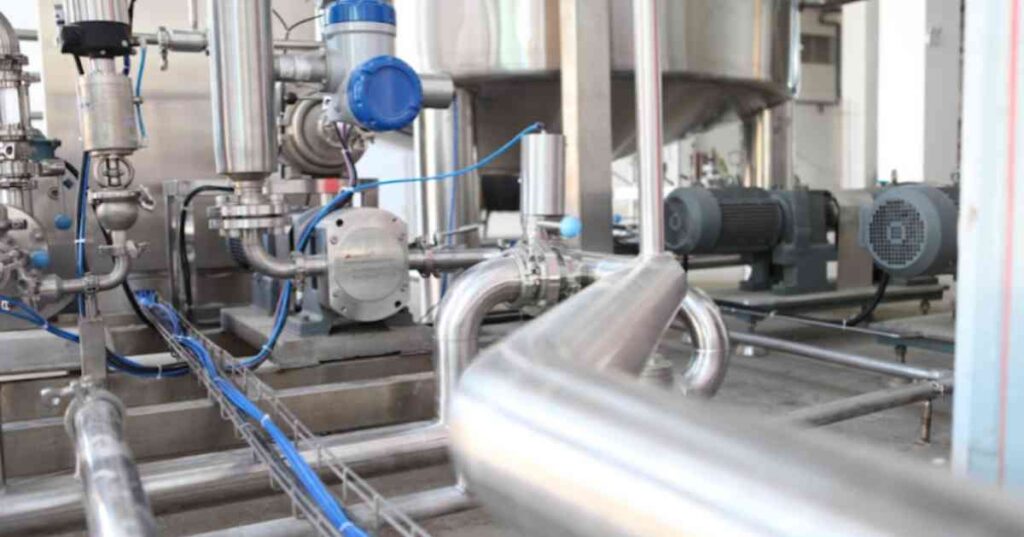
Even with diligent maintenance, industrial refrigeration systems can encounter common issues that must be promptly addressed. One of the most frequent problems is compressor failure, often due to overheating or inadequate lubrication. Identifying the signs of compressor distress early on, such as increased operating temperatures or abnormal sounds, can help prevent a complete shutdown.
Evaporator efficiency is another area prone to issues. The accumulation of frost or ice on evaporator coils is a typical concern that impedes heat transfer. Defrosting procedures should be part of the regular maintenance routine to ensure evaporators function optimally. A poorly performing evaporator can also signify broader system problems, such as incorrect refrigerant charge or airflow issues.
Another challenge is the management of condensate. If drainage systems are clogged or not functioning correctly, water can accumulate, causing damage to the system and increasing the risk of microbial growth. Ensuring condensate lines are clean and that water is effectively removed from the system is vital for maintaining refrigeration equipment health.
Altogether, the meticulous maintenance of industrial refrigeration systems is a multifaceted task that demands attention to detail, structured routines, and a commitment to ongoing education. The effort invested in proper maintenance will yield substantial benefits in reliability, efficiency, and service longevity, ensuring these critical systems continue to operate at their best.